Overview of Core Functional Technologies in Industrial Automation and Controls
Industrial automation and controls encompass a wide range of technologies that enhance efficiency, safety, and productivity in manufacturing and other industrial processes. Below is a detailed overview of the core functional technologies and effective application development cases in this field.
1. **Programmable Logic Controllers (PLCs)**
- **Functionality**: PLCs are robust digital computers used for automation of electromechanical processes. They can be programmed to perform a variety of tasks, including monitoring inputs, controlling outputs, and executing complex logic operations.
- **Application**: Widely used in manufacturing lines for tasks such as assembly, material handling, and process control.
2. **Human-Machine Interfaces (HMIs)**
- **Functionality**: HMIs serve as the interface between operators and machines, allowing for real-time monitoring and control. They display data visually and enable user inputs.
- **Application**: Commonly used in control rooms and on factory floors to provide operators with insights into machine performance and process status.
3. **Supervisory Control and Data Acquisition (SCADA)**
- **Functionality**: SCADA systems facilitate remote monitoring and control of industrial processes. They collect data from sensors and devices, allowing for centralized control and data analysis.
- **Application**: Utilized in utilities, oil and gas, and large-scale manufacturing to monitor and control operations over large geographical areas.
4. **Industrial Internet of Things (IIoT)**
- **Functionality**: IIoT connects industrial devices and sensors to the internet, enabling data collection, analysis, and remote management. This connectivity allows for smarter decision-making and operational efficiency.
- **Application**: Used for predictive maintenance, real-time monitoring, and enhancing supply chain visibility.
5. **Robotics and Automation**
- **Functionality**: Robotics involves the use of automated machines to perform tasks that require precision and speed. These systems can be programmed for various applications.
- **Application**: Common in assembly lines, packaging, and material handling, where they improve efficiency and reduce human error.
6. **Machine Learning and Artificial Intelligence (AI)**
- **Functionality**: AI and machine learning algorithms analyze large datasets to identify patterns, predict outcomes, and optimize processes.
- **Application**: Employed in quality control, predictive maintenance, and process optimization to enhance operational efficiency.
7. **Motion Control Systems**
- **Functionality**: These systems control the movement of machinery and equipment, ensuring precise positioning and speed control.
- **Application**: Used in CNC machines, conveyor systems, and robotic arms for tasks requiring high accuracy.
Effective Application Development Cases
1. **Automated Assembly Lines**
- **Case Study**: An automotive manufacturer implemented a fully automated assembly line using PLCs and robotics. This integration led to a 30% increase in production efficiency and a significant reduction in labor costs.
2. **Predictive Maintenance in Manufacturing**
- **Case Study**: A manufacturing plant integrated IIoT sensors to monitor equipment health. By leveraging machine learning algorithms for data analysis, they reduced unplanned downtime by 40% and extended equipment lifespan.
3. **Energy Management Systems**
- **Case Study**: A food processing company deployed a SCADA system to monitor energy consumption across its facilities. This initiative resulted in a 20% reduction in energy costs through improved load management and optimization.
4. **Smart Warehousing**
- **Case Study**: A logistics company implemented robotics and AI for inventory management. The use of automated guided vehicles (AGVs) and machine learning algorithms improved order fulfillment speed by 50%.
5. **Water Treatment Automation**
- **Case Study**: A municipal water treatment facility utilized SCADA and PLCs to automate chemical dosing and monitoring. This automation improved water quality and compliance with regulatory standards while reducing operational costs.
6. **Quality Control Systems**
- **Case Study**: A pharmaceutical company employed machine vision systems integrated with AI to inspect products on the production line. This approach reduced defects by 25% and significantly improved overall product quality.
Conclusion
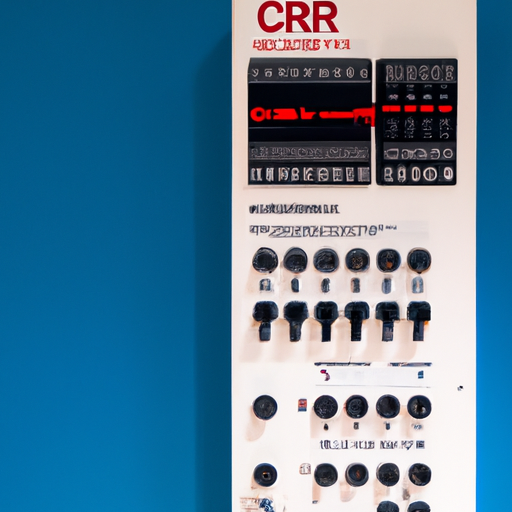
The integration of core technologies in industrial automation and controls has led to transformative improvements in efficiency, safety, and cost-effectiveness across various industries. The application development cases highlight the practical benefits of these technologies, demonstrating their potential to revolutionize operations. For specific insights related to the CFR-25JB-52-1K2 model, consulting industry publications, technical journals, or the manufacturer's documentation would provide more targeted information.